Cleaning In Place
Home > Applications > Cleaning In Place
Cleaning In Place (CIP) refers to the use of a combination of water, chemicals, heat and kinetic energy for a designated time to clean machinery, vessels, pipework or other contaminated equipment, without dismantling plant and without direct operator involvement.
When correctly applied CIP provides several benefits to the user including validated repeatable, cleaning performance, improved health and safety, reduced costs for labour and utility consumption.
The key to successful CIP is the design of automated systems which are effective at cleaning and repeatable in all possible circumstances. As CIP reliability has improved so has its application in increasingly demanding and highly regulated industries where hygiene and avoidance of contamination is paramount, including pharmaceuticals and bio-waste.
Suncombe provides superior quality cleaning-in-place (CIP) systems for the Biopharma industry, pharmaceuticals, and biotechnology sector. Using our advanced equipment alongside skilled technicians, they ensure efficient cleaning without dismantling. Cleaning In Place systems may be fixed in one location or mobile so as to facilitate several points of use. They may be designed as “total loss” systems, where the washing media is used once only before passing to drain or “recovery” systems, which recycle some of the washing media for part of the cycle.
SUNCOMBE & CIP (Clean-In-Place) systems
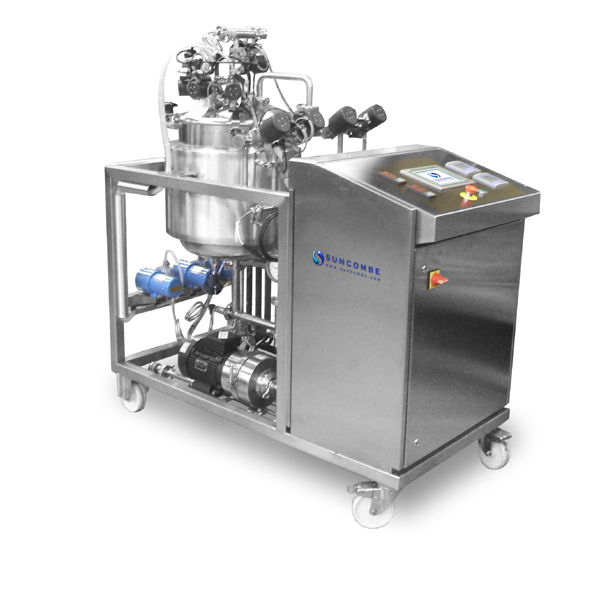
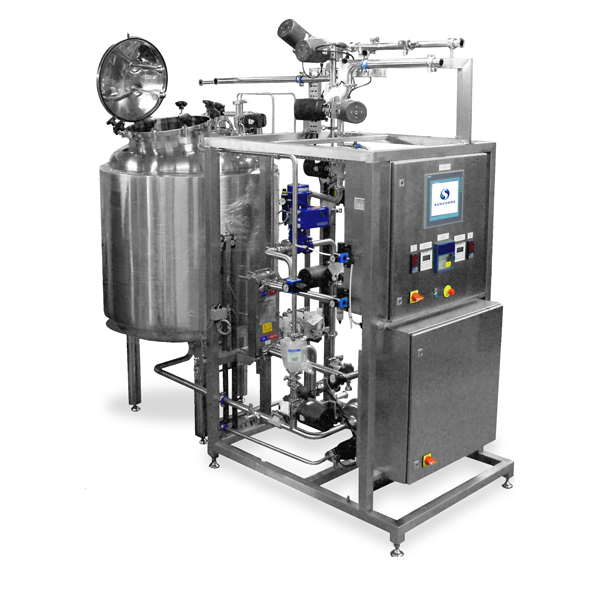
Suncombe pioneered the technology of CIP in the 1950s. Suncombe CIP Systems have been supplied for over 60 years and are used throughout the world in many different industries and sectors.
- First fully automated system installed in 1961
- 1,000s of systems used throughout the world
- 60+ years of design experience
- Developed with major clientele to meet their requirements
- Suitable for full validation
Suncombe specialise in addressing the most challenging applications which are often avoided by others. We have the knowledge, technology, products and experience to provide the complete CIP solution, including meeting complex project management, regulatory and validation requirements.
All CIP systems are made to Suncombe’s exacting sanitary manufacturing standards.
CIP – Using Energy for Cleaning
Cleaning uses a combination of thermal, chemical and kinetic energy applied for a set time. CIP allows higher thermal, chemical energies to be used for set times, thereby providing guaranteed repeatable cleaning.
Benefits of CIP (Cleaning in Place) Systems
The benefits of CIP over other cleaning methods include:
- Automated, repeatable, reliable and validatable
- Improved Health and Safety
- No/minimal equipment dismantling required
- Often improves cleaning times and reduces labour costs
- More effective using higher temperatures, stronger chemicals
CLEANING IN PLACE
Biotech CIP Targets
including:
- Chromatography columns
- Transfer lines
- Tangential Flow Filtration Units
- Centrifuges
- Bioreactors
- Mobile Vessels
- Depth Filters
- Hoses and Flexibles
- Valve Assemblies
Pharmaceutical CIP Targets
including:
- Tanks, Vessels, Intermediate Bulk Containers (IBCs)
- Vats
- Fermenters
- Glovebox Isolators
- Mixers Processors
- Pipework
- Flexibles
- Transfer Line Valves
- Fluid Bed Dryers
- Mills
- Coaters
- Filters
- Pumps
- Dryers
- Tumblers
- Fillers
- OEM Equipment
Other CIP Targets
including:
- Silos
- Incubators
- Powder Handling Systems
- Ducting
- Road Tankers
- Flowplates
- Pasteuriser
- Homogeniser
- Separator
- Blender
- Carbonator
- Heaters
- Coolers
- Valve blocks and manifolds
- OEM Equipment
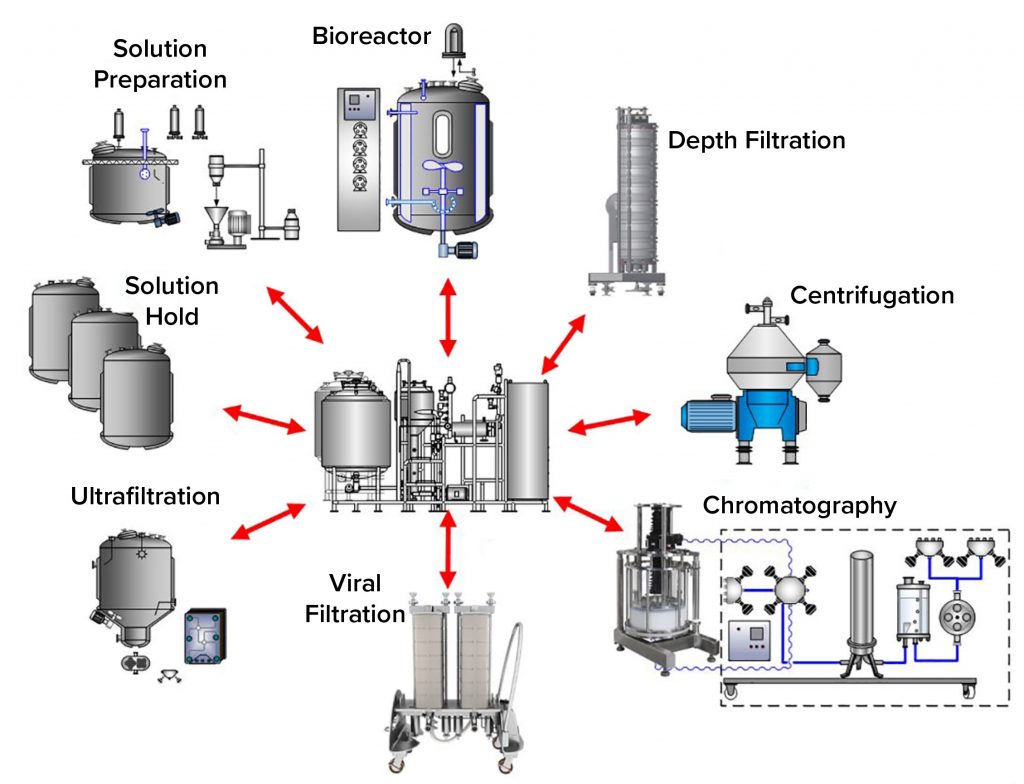