MOBILE (CLEANING IN PLACE) CIP
The Mobile CIP is a Total Loss cleaning in-place system supplied worldwide to BioPharma, healthcare, cosmetics, personal care, food, dairy, beverage and other processing industries. Designed and developed to be mobile to allow the entire system to be moved to its point of use. Manual or automatically operated, the WIP and CIP cleaning systems can be used for cleaning processing equipment including:
Tanks, Vessels, Vats, Fermenters, Mixers, Processors, Pipework, Valves, Isolators, Mills, Coaters, Filters, Pumps, Dryers and Fillers.
Built to hygienic and sanitary standards including ASME BPE, the MobileCIP™ incorporates a CIP buffer vessel for storing, batching and delivering CIP fluids, heating facilities, detergent dosing facilities, valving, pumps, instrumentation and an in-built control system.
Suncombe is among the leading global CIP system manufacturers in the UK catering to a diverse set of industries including pharmaceuticals, biopharmaceuticals, and biotechnology. Our state-of-the-art CIP system designs keep your equipment clean and hygienic, without the inconvenience of disassembly.
Leverage our advanced Mobile CIP systems and ensure excellent processing hygiene and sanitisation each time. Email [email protected] with your CIP requirements.
THE Mobile CLEAN-in-place system process
A Brief Overview of Our Mobile CIP Machine Process
The CIP cleaning system is an indispensable solution for biowaste, pharma, and biopharma producers, where hygiene and cleanliness can’t be compromised. Built as a total-loss CIP clean-in-place system, Suncombe’s Mobile CIP system effectively cleans and repeats the action as long as desired in an automated or manual fashion.
Our mobile clean-in-place equipment can be conveniently moved to multiple points of use in a facility. This ease of operation and movement facilitates efficient and thorough sanitation of piping systems and production equipment.
Suncombe’s Mobile CIP system covers multiple operations to ensure complete cleansing of production equipment. Depending on the level and extent of contamination, the cleaning stages include pre-rinsing, detergent cleaning, rinsing, acid cleaning, rinsing, disinfection, and final rinse.
We tailor the cleaning process according to your requirements, including the type of equipment material and the GMP and regulations to be followed.
Mobile CIP Cleaning System Product Range
Suncombe’s innovatively engineered CIP equipment makes it possible to ensure the utmost hygiene standards without compromising on your service. We offer multiple mobile CIP variants to suit our client’s requirements, each offering unique and key benefits:
MobileCIP®
Our ASME BPE Specification MobileCIP® is built for full validation, utilised worldwide by the biopharmaceutical industry. This CIP machine can be moved easily to the specific point of use. It incorporates a buffer vessel to store, batch, and deliver CIP fluids, heating, detergent, valving, pumps, and instrumentation, along with an in-built control system.
This Total Loss system consists of a 30 to 500-litre capacity single vessel to operate at an ambient temperature of 50 degrees Celsius. Our MobileCIP® skid design meets the most stringent and necessary sanitary and hygiene standards including ASME BPE.
MobileCIPOne™
Suncombe’s MobileCIPOne™ is a Total Loss Cleaning-In-Place system with a state-of-the-art design featuring 316 stainless steel hygienic delivery and scavenge pumps. We supply this mobile CIP system with no water storage or with the capacity to store 50 to 1000 litres of CIP solutions. This tank-based CIP system design delivers the CIP solution to the equipment in a controlled manner, while meeting the desired flow rate and pressure requirements.
The sanitary specification of MobileCIPOne™ is built for basic validation and used throughout the world in critical cleaning sectors such as healthcare, cosmetics, personal care, food, beverage, dairy, and other processing industries.
CIPTrolley
Utilising standard pre-approved modules, the CIPTrolley™ variant is a basic manual system that offers an economic solution to CIP whilst maintaining the quality of build and operation that Suncombe clients expect. Suncombe’s CIPTrolley™ systems comprise modules that clients can select and configure according to their requirements, along with the ability to exchange or add modules. This system offers multiple rinses including cold water rinse, hot water rinse, cold detergent rinse, hot detergent rinse, cold sanitiser rinse, drying, and air purge.
We can supply this system with one, two or three stainless steel tanks, with a capacity to store chemical solutions and cold or hot water drainage for up to 200 litres.
CIPWasher
The CIPWasher™ is a hybrid washer bringing the portability advantages of a high-pressure washer with the ability to apply the cleaning principles of a clean-in-place skid.
It’s an entry-level Clean-in-Place skid system that works similarly to a high-pressure washer to clean and sanitise pipes, tanks, hoses, and heat exchangers. This starter tank CIP system is ideal for smaller producers who want to start using CIP as well as for larger producers with equipment that is spread out. The hybrid delivery of CIPWasher™ includes water and chemical rinses, chemical rinse recirculation, liquid heating, and CIP suction to empty cleaned equipment.
To know which of our Mobile CIP variants is the right fit for your requirements, take a look at our Selection Guide or speak to one of our mobile cleaning-in-place (CIP) specialists.
SPEAK TO A MOBILE Cleaning in Place (CIP) SPECIALIST
How Mobile CIP’s Offer Flexible Cleaning in Place Solutions for Enhanced Portability and Efficiency
In industries where flexibility and portability are essential, such as the food and beverage, dairy, and brewing industries, mobile CIP (Clean-In-Place) systems have emerged as valuable assets. CIP (Clean-In-Place) systems are versatile cleaning solutions that offer the convenience of on-the-go cleaning, allowing for efficient and thorough sanitation of equipment and piping systems in various locations.
Mobile CIP equipment is designed to be compact, portable, and easy to manoeuvre. They are equipped with wheels or casters, enabling operators to move the system to different areas of the facility as needed. This flexibility eliminates the need for dedicated fixed cleaning stations, saving space and accommodating diverse cleaning requirements across the production facility.
Key Advantages of Suncombe’s Mobile CIP Cleaning Systems
One of the primary advantages of Suncombe’s mobile CIP systems is their ability to deliver efficient and reliable cleaning performance in different settings. Whether it’s cleaning tanks, pipes, valves, or other equipment, these systems provide a comprehensive solution to remove residues, contaminants, and biofilms from surfaces. By utilising a combination of cleaning agents, temperature, and flow rate, our mobile CIP Cleaning systems in the UK, US and across the globe ensure thorough and consistent cleaning, minimising the risk of contamination and product defects.
Suncombe’s Mobile CIP systems offer ease of use and convenience for operators. They are designed with user-friendly interfaces and intuitive controls, simplifying the setup, operation, and monitoring of cleaning cycles. Operators can easily adjust cleaning parameters, such as temperature and cleaning agent concentration, to meet the specific requirements of different equipment and products. This adaptability enhances the efficiency of cleaning processes and allows for customization based on varying cleaning needs.
Read More
Furthermore, our mobile CIP systems are equipped with efficient resource management features. They optimise the use of water, cleaning agents, and energy, minimising waste and reducing operating costs. These systems may include recirculation systems, variable speed pumps, and sensors to ensure precise control over resource usage. By promoting sustainable practices and resource efficiency, Suncombe’s mobile CIP equipment aligns with environmental stewardship goals and supports responsible manufacturing.
Mobile CIP machines in the US, UK and worldwide also incorporate safety features to protect operators and maintain a secure working environment. They may include safety interlocks, emergency stop buttons, and integrated safety protocols to prevent accidents or mishaps during cleaning operations. Additionally, these systems are designed to meet relevant regulatory guidelines and quality standards, ensuring compliance with industry requirements.
In conclusion, our mobile CIP systems offer flexible and efficient cleaning solutions for industries that require portable sanitation capabilities. With their compact design, ease of use, and resource optimization features, these systems enhance operational efficiency, reduce downtime, and ensure product quality and safety.
Implementing mobile CIP systems enables manufacturers to maintain cleanliness and hygiene standards across various locations, enhancing overall productivity and customer satisfaction. Invest in Suncombe’s mobile CIP systems today to unlock the benefits of flexibility and efficiency in your cleaning processes. We can provide you with a CIP (Clean-In-Place) system that is customised and fits your specific needs!
Call us or email [email protected] for more information.
We can offer a range of standardised cleaning in place systems built to a specification to suit your needs. Each of the below CIP & WIP Systems can be specified to one of our variants
Part # | Tank Volume Litres | Flowrate Litres per minutes | Head Pressure barg | Dimensions A (mm) | Dimensions B (mm) | Dimensions C (mm) |
---|---|---|---|---|---|---|
MobileCIP™60 – 1 Tank | 150 | 60 | 4.5 | 1,750 | 850 | 1,900 |
MobileCIP™60 – 2 Tank | 2 x 150 | 60 | 4.5 | 1,750 | 850 | 2,350 |
MobileCIP™60 – 2 Tank – Square | 2 x 150 | 60 | 4.5 | 1,750 | 1,400 | 1,400 |
MobileCIP™100 – 1 Tank | 250 | 100 | 4.5 | 1,950 | 1,050 | 2,050 |
MobileCIP™100 – 2 Tank | 2 x 250 | 100 | 4.5 | 1,950 | 1,050 | 2,550 |
MobileCIP™150 – 1 Tank | 350 | 150 | 4.5 | 1,950 | 1,050 | 2,250 |
MobileCIP™150 – 2 Tank | 2 x 350 | 150 | 4.5 | 1,950 | 1,050 | 2,850 |
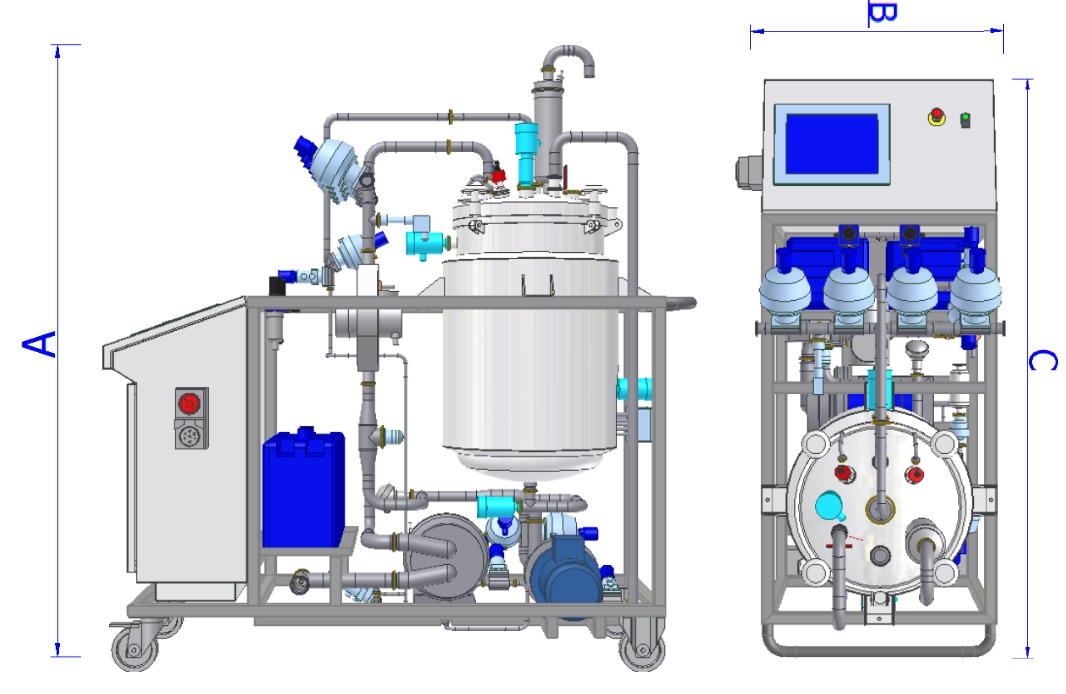
SIP capabilities available in all of our Mobile CIPs. The sterilisation of production equipment carried out by the means of superheated steam.
ATEX versions are available for solvent use and/or aqueous use in zoned areas
Optional stainless steel covers can be fitted
Buffer vessel for solution mixing
Includes dosing confirmation which can be incorporated within any recipe step at any concentration
Different purities of water from WFI (water from injection to towns water)
Sanitary and sterile processing routing and Biopharma diaphragm valves
High quality analytical and process instrumentation
Available with conductivity controllers for detergent concentration and pure water.
High power electrical liquid heating for fast heat up times
Build your own operational method/process
Fully self-draining including pump housing
Operator Friendly and intuitive system
If you feel your line of questioning falls outside of our custom form you can contact one of our specialists by:
Phone: +44 (0) 208 804 5555
Email: [email protected]
We are able to accommodate multiple user requirements, and are experienced in designing and manufacturing systems to various specification variables. To quickly generate an enquiry with us fill in the below form with as much detail as available to you, the form will auto-submit with your initial enquiry. This will enable our experts to begin assessing your system requirements and a sales representative to open a clear and concise channel of communication with you.
If you feel your line of questioning falls outside of our custom form you can contact one of our specialists by:
Phone: +44 (0) 208 804 5555
Email: [email protected]
We are able to accommodate multiple user requirements, and are experienced in designing and manufacturing systems to various specification variables. Quickly fill out your information in the form below so one of our team members can help you with your specific requirements.
ASME BPE standard Pipework, fully annealed, chemistry to ASTM A-269, manufactured to ASTM A-270, and 3A Standard.
316 Stainless steel product contact parts, 304 non-contact parts, Hastelloy and Duplex Stainless.
T.I.G Welding; using argon gas purge, using a computer controlled enclosed head orbital welding plant.
PED Vessels, Complete material traceability, PD5500 compliant.
European Hygienic Engineering and Design Group (EHEDG)
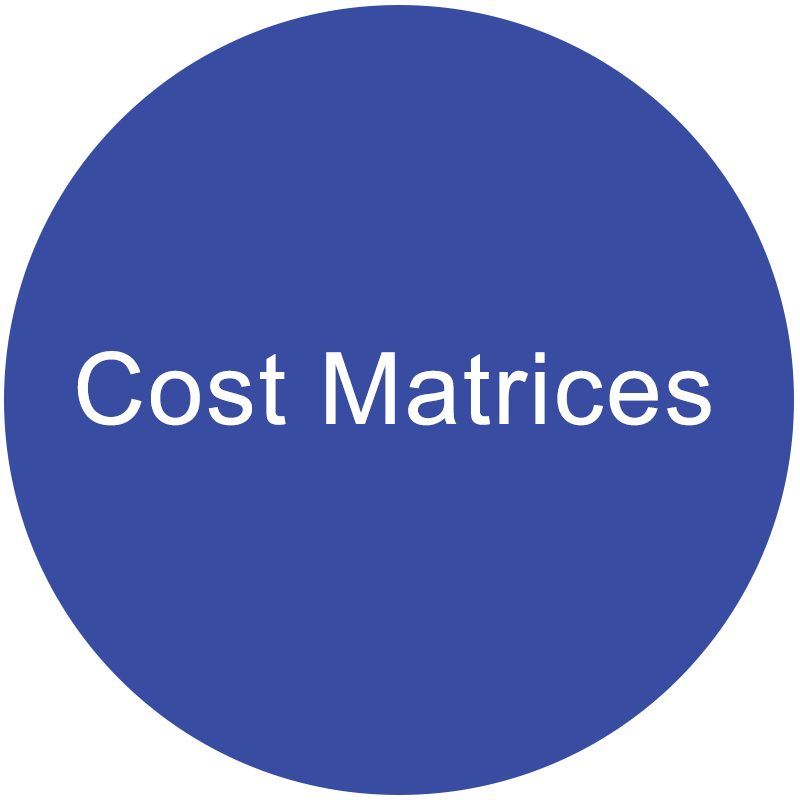
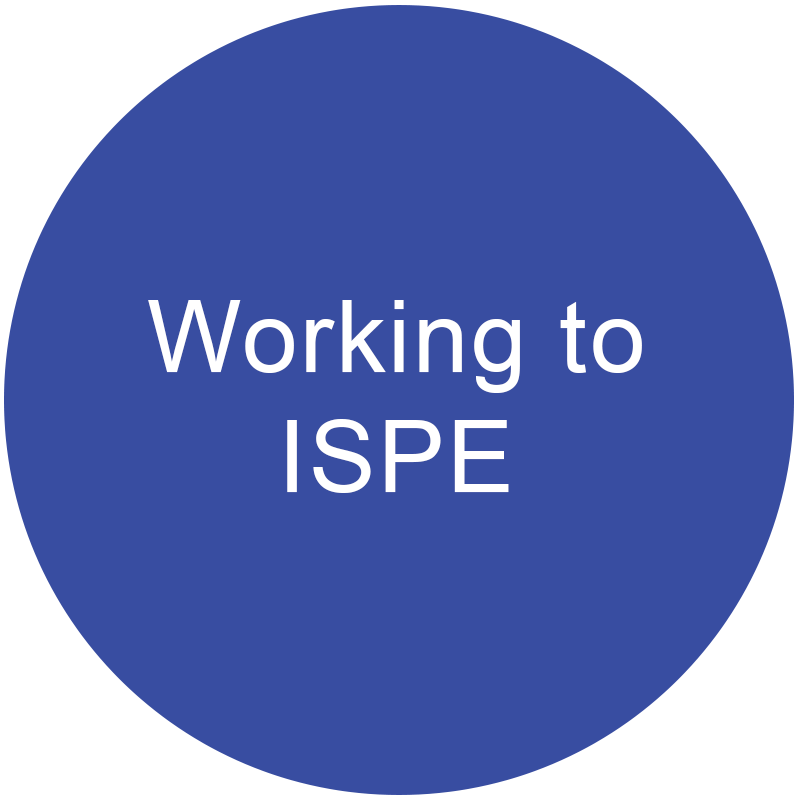
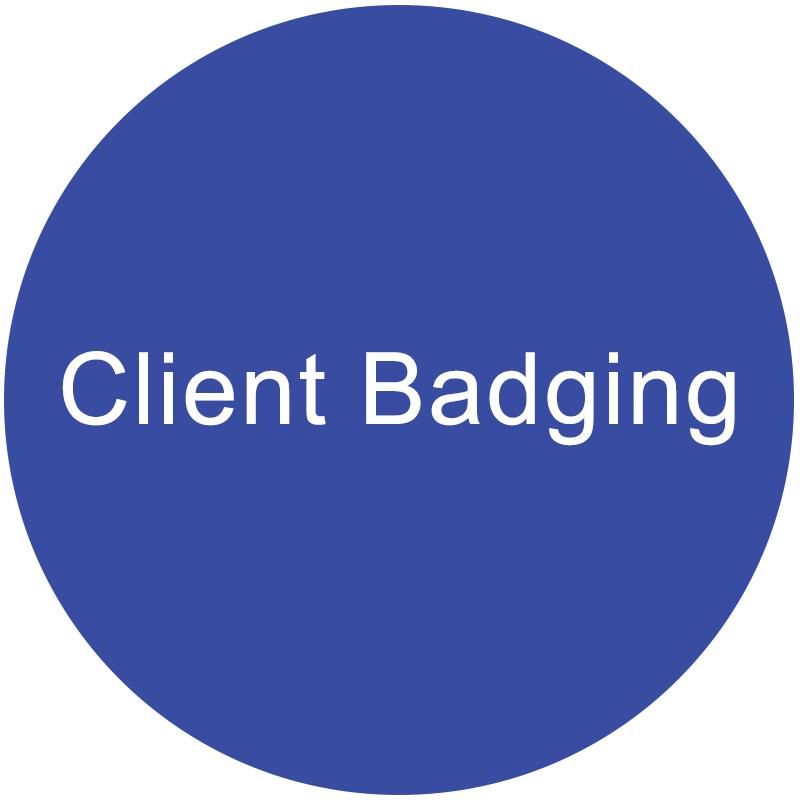
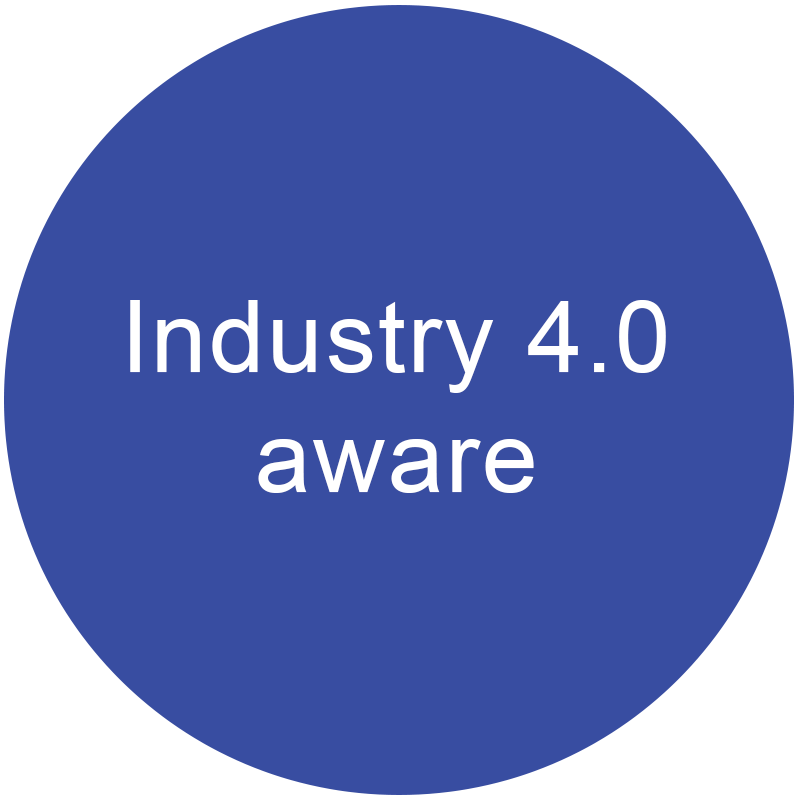


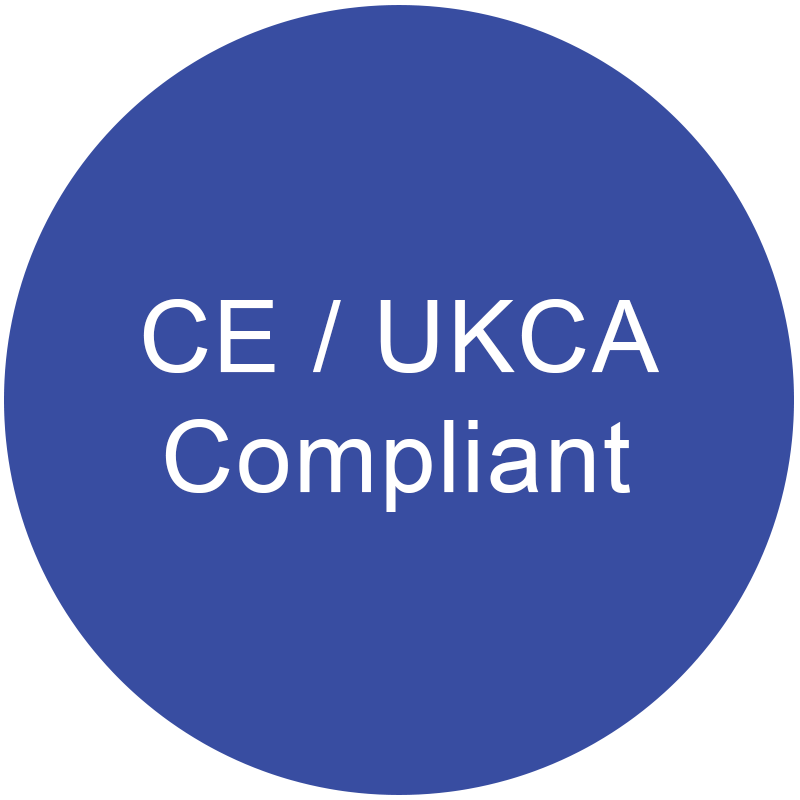
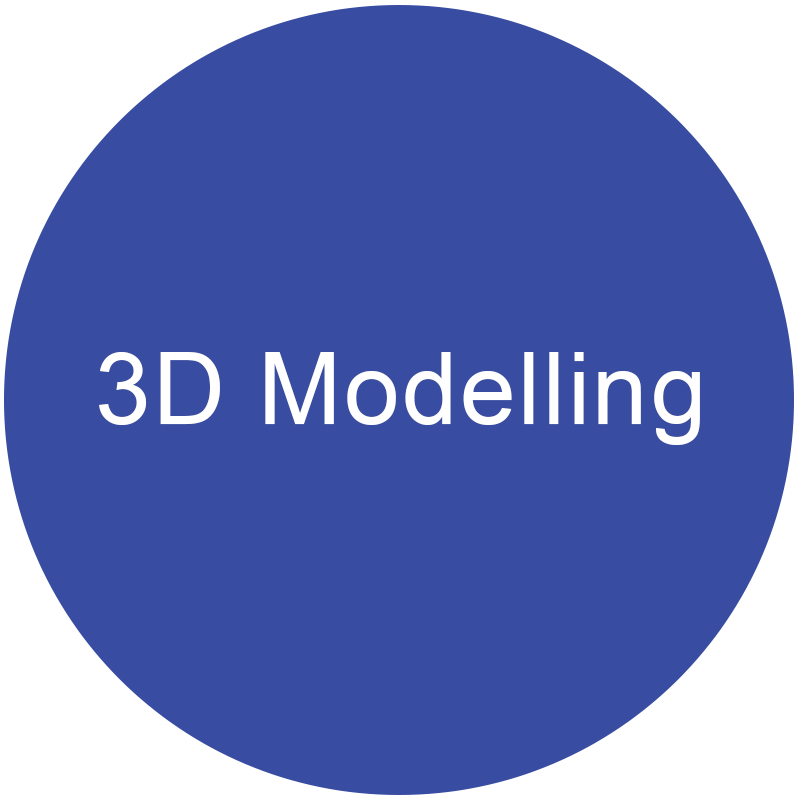
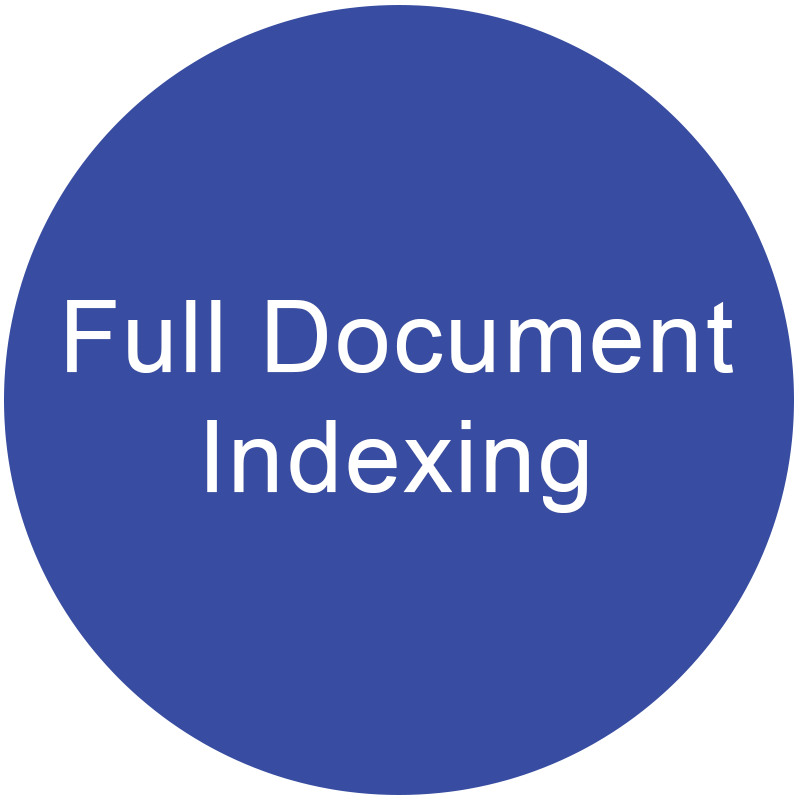
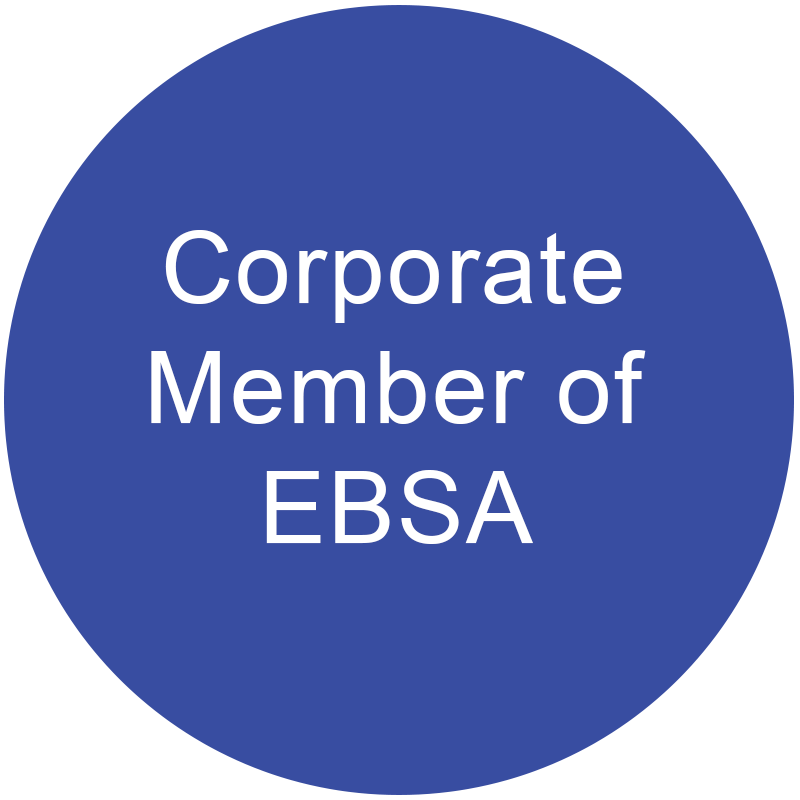
Cost Matrices
Client Badging
GAMP
CE Compliant
Full Document Indexing
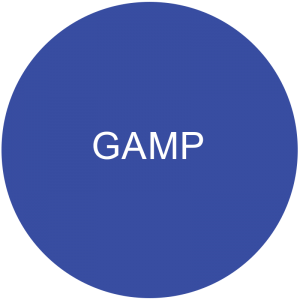
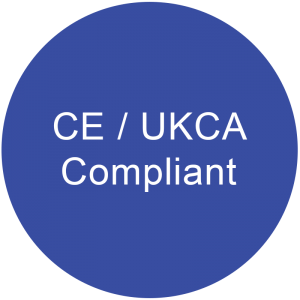
Working to ISPE
Industry 4.0 Ready
Data Manuals
3D Modelling
Corporate member of EBSA
Welding Standards
- BS EN 10204 – 3.1
- BS EN ISO 9606-1:2013
- BS EN ISO 15614-1:2004+A2:2012
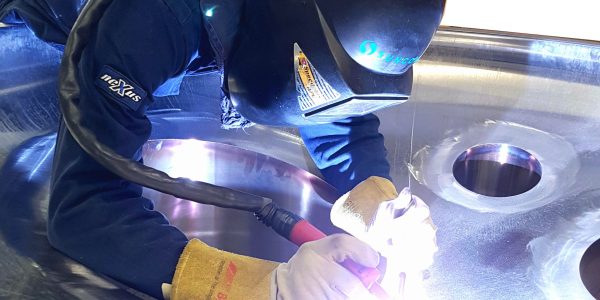
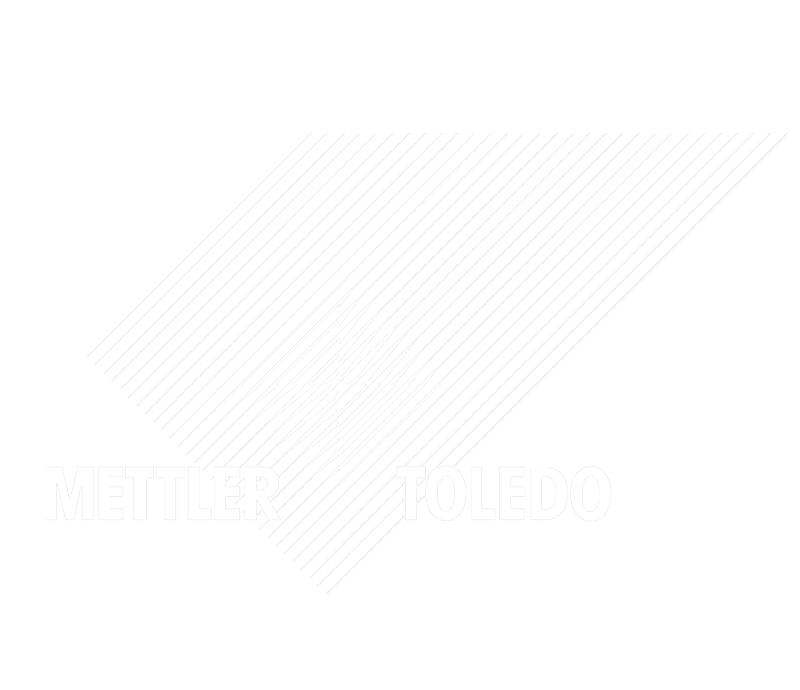
Mettler Toledo
Why Choose Suncombe?
A frontrunner in cleaning-in-place system design since the 1950s, Suncombe LTD has established itself as a market leader in the CIP and WIP space. We are committed to continuously improving through innovation, fueling our endeavour to excel and exceeding our client’s expectations each time. Our Mobile CIP system variants are just a small percentage of our superior product range and services in CIP systems.
Suncombe is immensely proud of being the oldest and among the most trusted biowaste and CIP system manufacturers in the UK, US, and across the world. Our core values of innovation, engineering accountability, automation, and business partnership uphold our legacy and position us above the competition.
Partner with us for a reliable and technologically advanced manufacturer and service provider of CIP cleaning systems in the UK, the US, and the rest of the world.
Email [email protected] or call +44 (0) 203 089 0280 to speak to one of our specialists.