The Suncombe IsolatorCIP ®
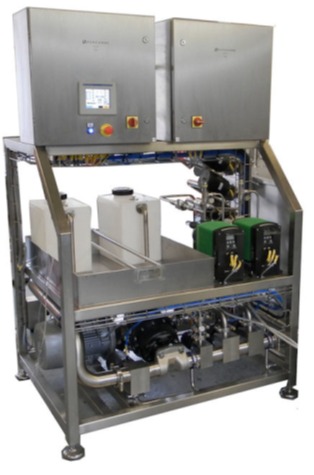
CIP and WIP for Glovebox Isolators
CIP and WIP systems are integral for maintaining hygiene and efficiency in glovebox isolators. Our cutting-edge CIP clean-in-place system ensures thorough cleaning without disassembly, optimising workflow. Additionally, our WIP system facilitates seamless washing of internal components, guaranteeing cleanliness and minimising downtime. With our comprehensive solutions, glovebox isolators remain compliant and operational, meeting stringent industry standards. Trust in our expertise to deliver reliable CIP and WIP systems tailored to your specific requirements, ensuring peak performance and safety.
After the initial development and release of the IsolatorCIP® in the early 2000’s, numerous systems have been provided to worldwide biopharma clients for many different Glovebox Isolator manufacturers. Throughout this period, the IsolatorCIP® have been subject to a Continuous Development Programme and after nearly 20 years, these have now been incorporated and the IsolatorCIP® re-released for the 2020s. Incorporating innovative and novel methodologies, the IsolatorCIP® was developed following industry demands, to provide a bespoke solution, allowing reliable, repeatable and validatable CIP and WIP of Isolators and Gloveboxes.
Traditionally Glovebox Isolators have been manually cleaned however automatic cleaning by using a Cleaning In Place or Washing In Place System, optimises the repeatable cleaning process to reduce the percent of cross-contamination after each use and remove any product or debris. The IsolatorCIP® was developed to provide this automatic Cleaning In Place and Washing In Place System, whilst removing the need for the disassembly of the isolator in the process.
Glovebox Isolators are used to allow a person to Handles and process hazardous or toxic substances in a contained environment. They provide bespoke barrier containment solutions that allow for protection of both the user and the product. The user can thus carry out hands-on, manual processes such as dispensing, sampling and product pack-off of products as well as contained processing operations. Reasons for Isolator usage trends include Increased potency of drug compounds, reducing operator exposure levels, smaller volume/higher value pharmaceutical production and Instead of setting up a whole cleanroom, isolators provide a smaller, more controlled and more adaptable environment.
Designed for aqueous, detergent and/or solvent cleaning, the IsolatorCIP® was developed to incorporate “Lean Manufacturing Principles” ensuring that generation of waste is minimised whilst efficiency is maximised.
The Suncombe IsolatorCIP® is designed to provide an automatic, repeatable cleaning sequence which can be individually configured to include different water qualities, chemicals, detergents and sterile hot, cold and dry air streams. These can be provided at accurately controlled temperatures, flowrates and pressures, to ensure the optimum clean is achieved. The systems are also available in hazardous versions, designed for use in ATEX areas and for delivering solvents for wet down purposes.
Utilising variable recipe-derived configurations, the IsolatorCIP® can also be used to effectively clean additional processing equipment enclosed inside the isolator or fitted onto the in-feed or discharge sides. Incorporating replaceable modules, the base unit is a fully hygienic version, with optional modules for sterile use including sanitising and sterilising configurations.
Steve Overton, Technical Director at Suncombe commented: “The new versions of the IsolatorCIP® reflect changes in the product including a full suite of environmental considerations providing improved sustainability, to reflect the changes throughout the Suncombe product ranges. The systems are all tailored to suit different specific requirements and incorporate containment methodologies and are designed around ASME BPE, FDA 21CFR11, cGMP, GAMP and ATEX requirements.
Suncombe’s IsolatorCIP® systems can be integrated with isolators of any manufacturer, with pre-configured mechanical and control interfaces, they minimize the potential for cross contamination and downtime whilst at the same time ensuring the total protection of personnel. The machines themselves are manufactured from 316L certified stainless steels and incorporating high quality components, they are fabricated by qualified technicians to certified procedures. Incorporating a user-friendly colour touch screen, they provide the optimum control of the entire process using an easily configured recipe structure and provide confirmation at the successful completion of cycle. Remote control facilities can be incorporated for interfacing to the Isolator control systems.
Complementing our extensive range of Cleaning In Place Systems, BioWaste Decontamination Systems, GMPWashers and Process Suites, the new IsolatorCIP® is manufactured in the United Kingdom and is available worldwide through our sales networks.