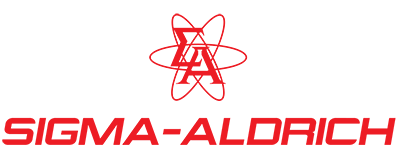
Sigma-Aldrich (SAFC) Expansion in Irvine, Scotland
The company
The Facility – courtesy of SAFC Irvine
SAFC Irvine is the centre of excellence for the manufacturing of liquid media, buffers and reagents used in the biopharmaceutical industry. The 11,000 m2 cGMP facility consists of liquid production facilities capable of producing a broad range of batch sizes, quality control laboratories and dedicated Temperature controlled raw materials and finished goods warehousing. A new Dry Powder Media (DPM) manufacturing facility was constructed and qualified at the existing site. The addition of dry powder milling and blending capability to this facility will complete a 5-year Capital Expansion Plan SAFC initiated as part of its long-term commitment to supporting customers in the growing industrial biopharmaceutical market. The purpose-built facility will produce animal component free (ACF) media and will offer regional support to the European market along with manufacturing redundancy to its North American sister facility in Lenexa, Kansas.
GMP Purified Water Distribution Skid
pH Neutralisation System
The project
Suncombe was asked to provide a number of items of process equipment for the new plant, including a Purified Water Handling Skid to distribute purified water around the new plant; a Cleaning In Place System (CIP) which incorporated two CIP pressure vessels, the ability to dose two chemicals in line and control the temperature for CIP’ing vessels, pipelines and equipment in the new production process; an Immersion Washer to allow site to wash miscellaneous parts in a repeatable manner; and a pH neutralisation system incorporating 2 x 9000 litre storage tanks to accept site effluent and neutralise the waste pH prior to discharge. All of this equipment was designed and manufactured specifically to suit SAFC’s requirements and was constructed to standards including ASME BPE and GAMP, to allow full validation.
GMP Immersion Washer for Washing Parts
Our Approach
Following receipt of detailed design criteria, the Suncombe engineering team developed customised equipment, based around our standard methodologies. The developments were provided to SAFC for their input prior to the manufacturing stages. An extensive interface arrangement was incorporated to allow the integration of the Suncombe equipment into their factory wide control system. The construction programme was finished on schedule and there followed Factory Acceptance Testing, carried out to pre-approved testing protocols, to allow SAFC full visualisation of the operation of the new equipment. These extensive predelivery tests were carried out to ensure that on delivery to site the system was pre-tested ensuring that reconnection and preparedness for operation was straight forward. Following delivery and installation, the testing regime continued with the next stage of Site Acceptance Testing, once again against pre-approved protocols. Tests were carried out to prove that the installed system maintained the operation of the Factory Accepted system and seamlessly went into process operation.
Suncombe Comments
Elliott Sutton, Automation Manager at Suncombe, commented, “It was a very fast-paced, exciting and challenging project. We enjoyed working with a large team from different companies and disciplines and achieved great satisfaction on the successful implementation and integration in a number of different items of Suncombe equipment.”
GMP CIP Skid